Wir alle kennen den Effekt: Zu Beginn funktionieren Elektrogeräte mit Akku noch super, doch über die Lebensdauer wird die Akkulaufzeit immer kürzer, bis manche Akkus dann völlig den Dienst quittieren. Hierzu muss man wissen, dass die meisten Akkus nicht aus einer einzigen Zelle bestehen, sondern eine komplexe Reihen- und/oder Parallelschaltung von einzelnen Akkuzellen sind. Jeder Akku altert jedoch leicht unterschiedlich und so ist es vereinfacht gesagt wie in einer Kette: Das schwächste Glied bestimmt die Gesamtkraft, die die Kette aufzunehmen fähig ist – im Akku dann eben die Laufleistung. Wobei dies nicht 1:1 stimmt, denn in Li-Ionen-Akkus haben sog. Balancer-Elektronik verbaut, die versucht, die unterschiedlich schnell alternden Zellen möglichst lange gemeinsam harmonisch gemeinsam arbeiten zu lassen, bis dies an seine Grenzen kommt. Es gibt also viele Gründe, warum z.B. ein Ebike oder Laptopakku oder auch eine Powerbank nur noch stark eingeschränkt Energie liefert: Mal ist es nur eine einzige defekte bzw zu schnell gealterte Zelle aus einem Verbund von 5 oder mehr (im E-Bike-Akku teilweise 50 oder mehr) Zellen, die die Gesamtleistung des Akkus ruiniert, es können aber natürlich auch alle Akkus gemeinsam sein, die hier den Akku „schwach“ erscheinen lassen. Ich habe aber auch schon Akkus gefunden, in denen alle Zellen noch 1A waren, die Balancer-Elektronik jedoch defekt war…
E-Auto-Akkus leiden übrigens unter dem gleichen Problem und hier entwickelt sich gerade eine Industrie, die genau dieses Problem angreifen wird: Reparieren statt wegwerfen, geschickt selektiv recyceln statt verbrennen, deponieren oder zerlegen. Wenn wir heute eine neue Bleibatterie als Starterbatterie für ein Auto kaufen, so ist diese zu sehr großen Anteilen aus bereits recycelten Batterien hergestellt worden. Für Lithium-Ionen Akkus steht diese Recycling-Kette noch in den Kinderschuhen und es war mir eine große Freude, hier eigene Pionierarbeit leisten zu können und zig ausrangierte und auf ebay erworbene Laptopakkus zu öffnen, zerlegen, durchzumessen und prüfen zu können. Meine Recyclingquote lag bei ca. 27%, d.h. ich habe in etwa 3 gebrauchte Akkuzellen aussortiert, um eine einzige brauchbare Akkuzelle zu erlangen. Für meine 200 verbauten Zellen habe ich also exakt 740 Zellen aussortiert, pro Laptop sind ca. 6 Zellen im Durchschnitt verbaut, das heißt ich habe über 150 Laptopakkus geöffnet und zerlegt. Die Auswahl der Zellen wurde über die Messung des Innenwiderstandes und der verbleibenden Restkapazität getätigt, wenn beide Werte nah am Original bzw. von mir festgelegten Grenzwerten lag, so wurde eine Zelle als brauchbar klassifiziert und in meinem Solarbike-Projekt verbaut.
Als Grenzwert für den Innenwiderstand habe ich 75 mOhm definiert, denn Zellen, die darüber liegen, hatten meist schon sehr reduzierte Kapazität und auch einige Zyklen. Es gibt Untersuchungen, die zeigen, dass der Innenwiderstand einer Akkuzelle direkten Aufschluss über die Zahl der Zyklen und Restlebensdauer, die von de Zelle noch zu erwarten sind bzw. bereits hinter sich hat.
Nach dem Test des Innenwiderstandes wurde die Kapazität der Zelle getestet, allerdings (ganz wichtig!) im Entlademodus. Im Lademodus geht Energie in Hitze verloren (Ladeverluste), die hier gemessene Ladungsmenge ist also nicht die real nutzbare Kapazität der Zelle. Einzig der Entlade-Kapazitätstest gibt die real nutzbare Kapazität der Zelle an. Die Zellen wurden dann über einen Monat gelagert und getestet, ob sie die Spannung halten. Die Zellen wurden in Gruppen von +/- 50mAh Kapazität gruppiert, damit jeder Block des Akkus eine möglichst ähnliche Gesamtkapazität hat. Ein Block des Akkus besteht aus 20 parallel verschalteten Zellen und wieder 10 dieser Blöcke wurden in Reihe geschaltet, um die 36V Systemspannung zu erreichen. So ergibt sich eine sog. Konfiguration von 10s20p (10 seriell verbundene Blöcke mit je 20 parallel verschalteten Zellen).
Die neuen Akkuhalterungen hat mein 3D-Drucker aus PLA gedruckt (Vorlage https://www.thingiverse.com/thing:4604383) und letztendlich habe ich alles mit Isomatten gefedert in einer Holzkiste verstaut.
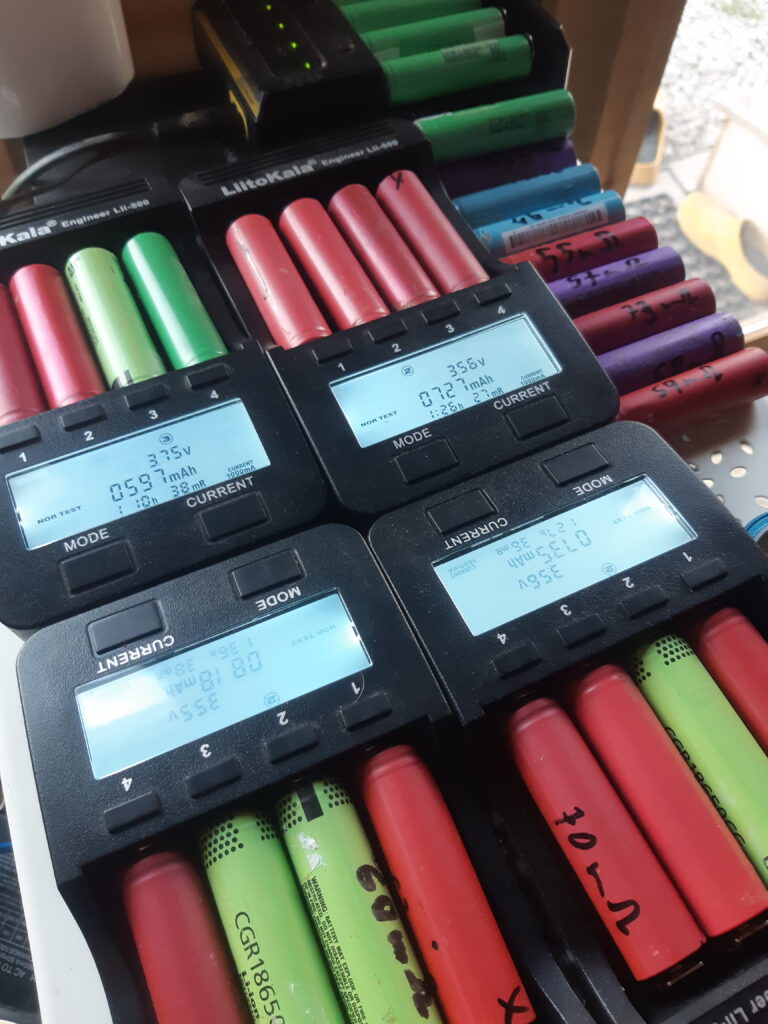
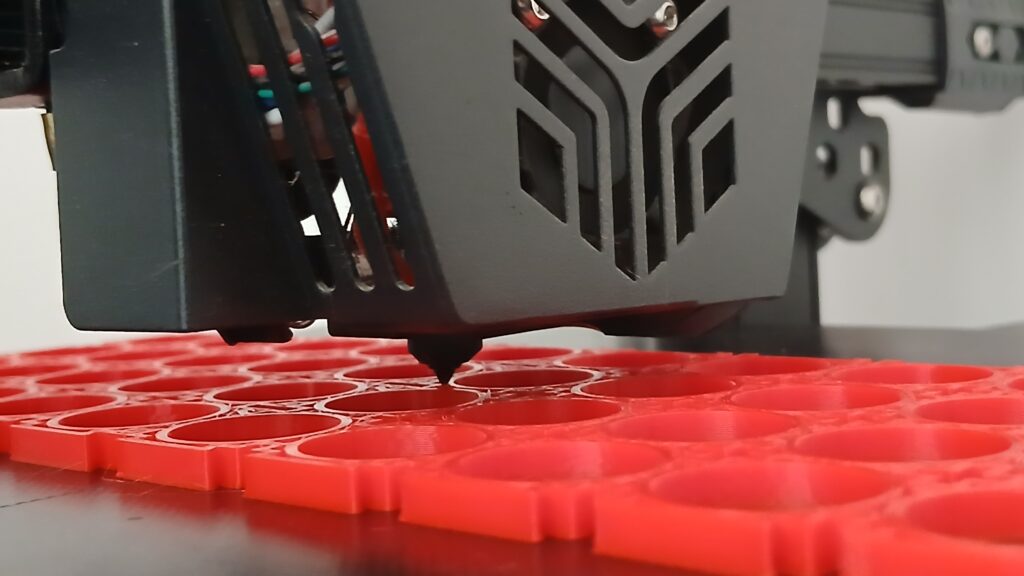
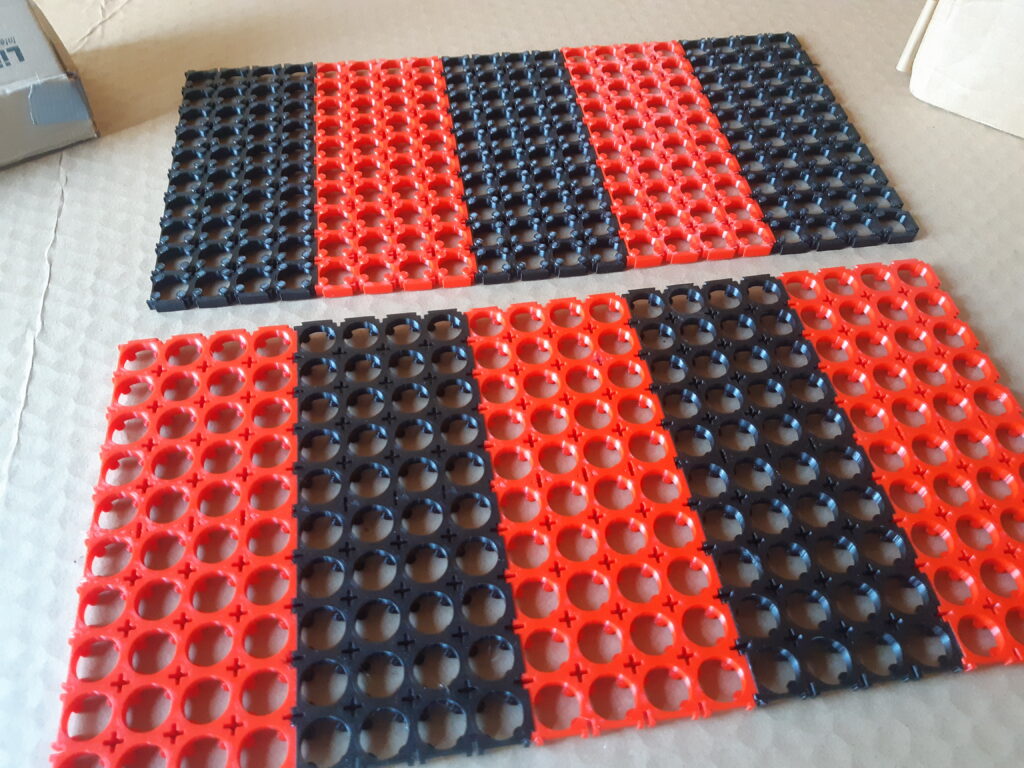
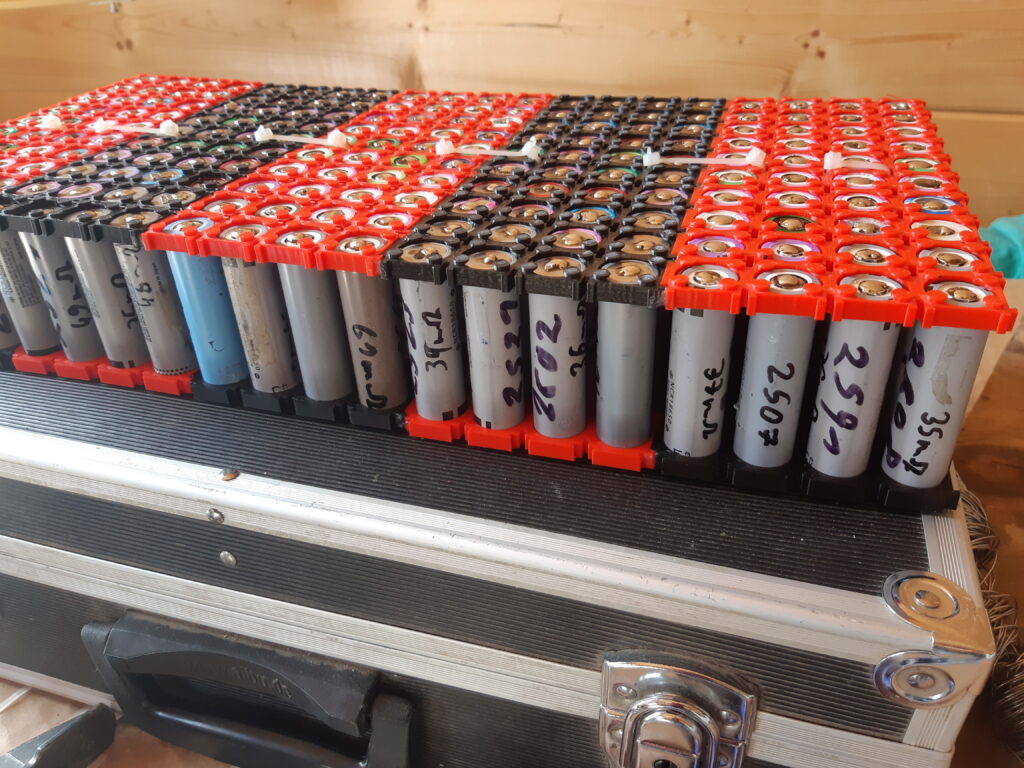
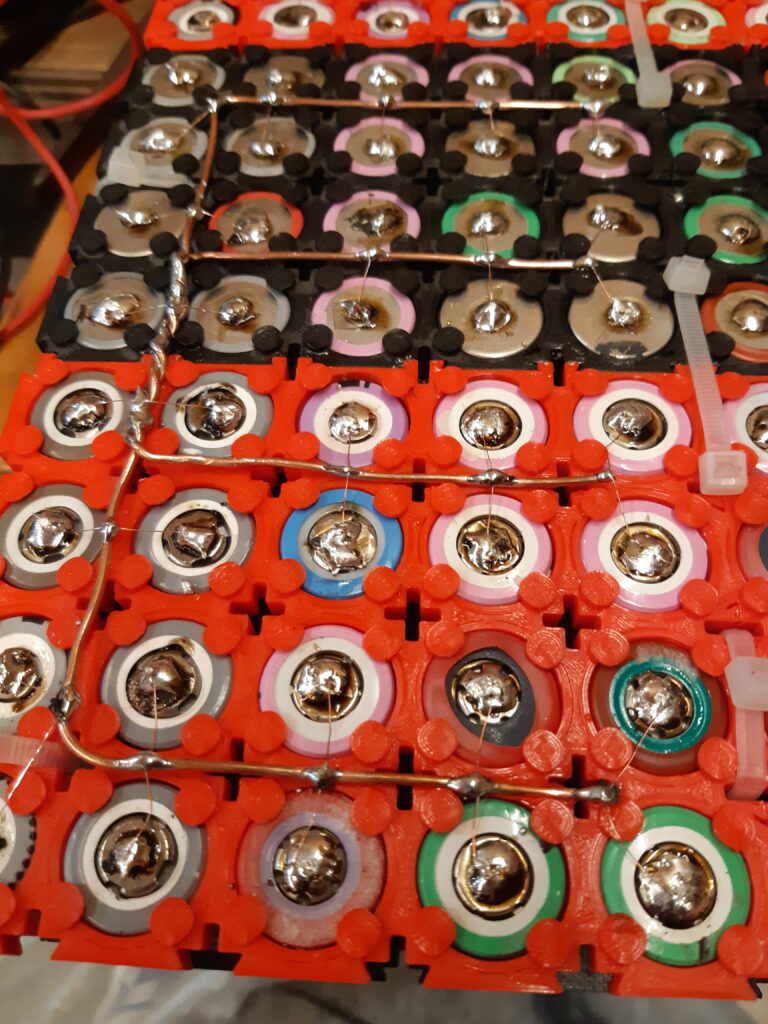
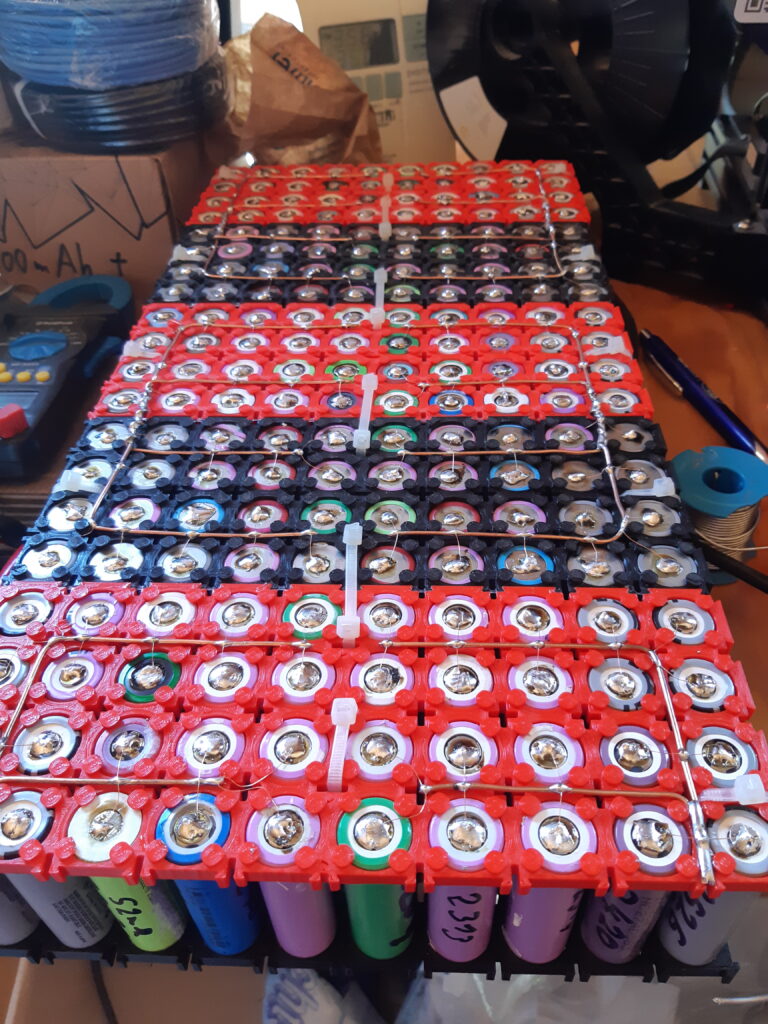
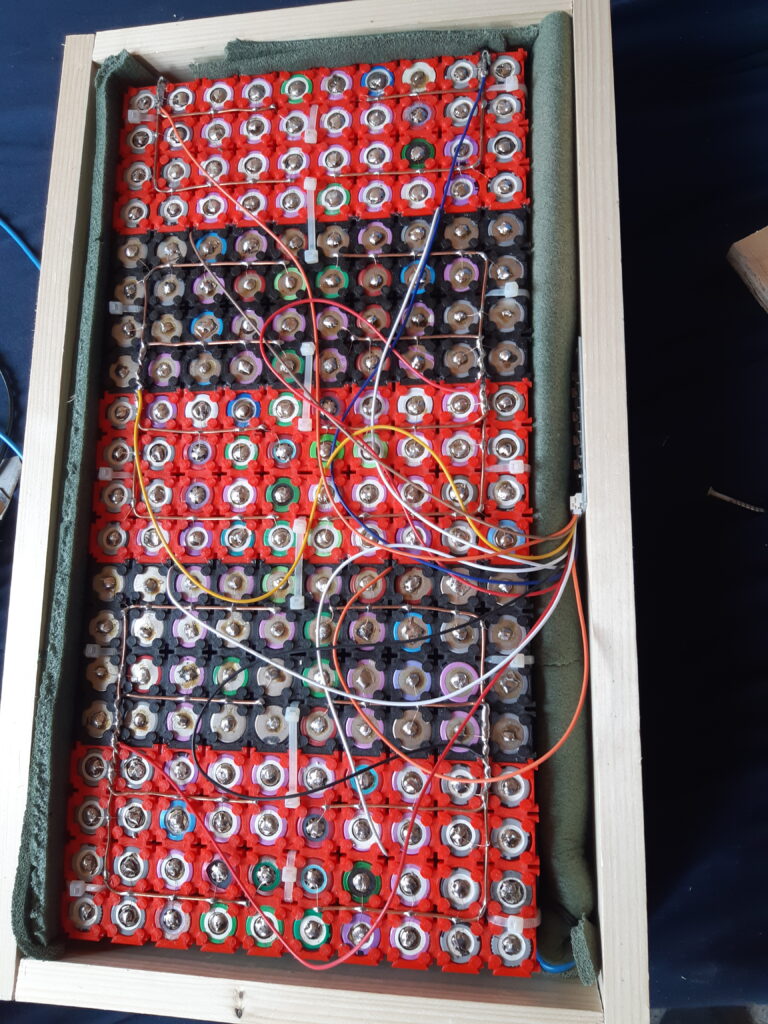